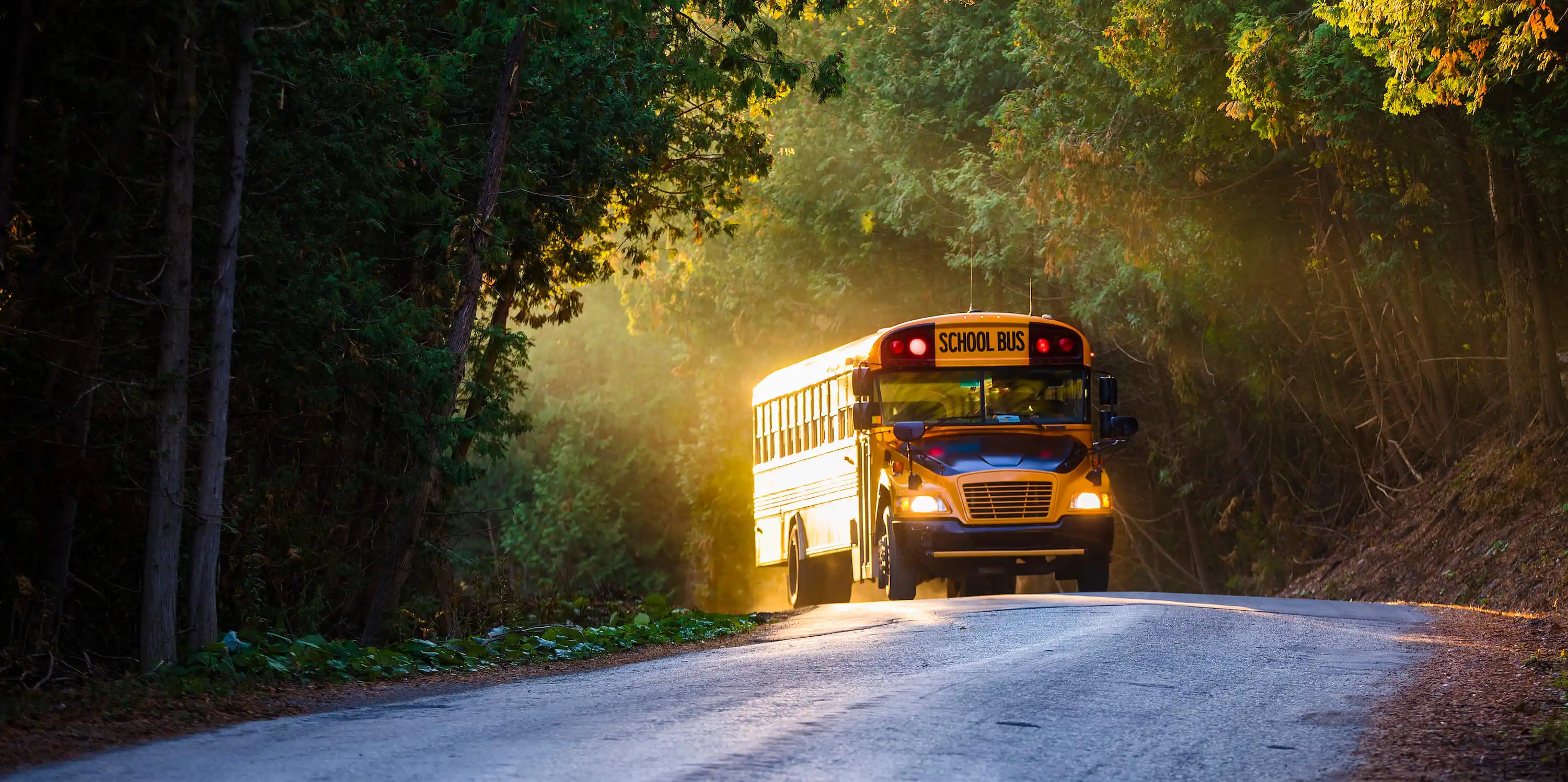
How To Use This Planning Guide
This Electric School Bus (ESB) Planning Guide provides a step-by-step process for bus fleet electrification. Users can start at the beginning or dive into a specific step given their individual needs.
If you have questions or need assistance outside of the information provided here, the Joint Office of Energy and Transportation has partnered with the U.S. Environmental Protection Agency to provide FREE technical assistance to school bus fleets that are eligible to apply for Clean School Bus Program funds. To receive technical assistance, reach out to cleanschoolbusTA@nrel.gov or fill out the contact form.
Phase One: Learn
Overview: Learn
The first phase of this guide will introduce you to the basics of school bus electrification and help you prepare for phases two and three: scope and plan. The resources provided in this phase will help you:
- Understand the basics of electric school buses and charging
- Gauge organizational and community support
- Define your goals
- Identify and coordinate your team.
Step 1 - ESB Basics
Aside from the electric powertrain, ESBs are very similar to conventional buses. Fleets should select a model that meets their existing safety regulations, size, and other requirements. The video series Flipping the Switch: Electric School Bus Introduction contains helpful information on the basics of adopting ESBs. Major considerations unique to ESBs include:
Battery Size: ESB batteries are rated in kilowatt hours (kWh). Larger batteries will typically equate to increased range.
Range: Depending on the model, ESBs can travel up to 150 miles on a single charge. Range will be impacted by operator driving style, heating and cooling use, terrain, and payload. Driving ranges provided by manufacturers are usually calculated for ideal operating conditions.
Bus Efficiency: The bus battery size (kWh) divided by the range (miles). A lower kWh/mile value indicates a more efficient bus.
Effect on Range: Heating and cooling needs will impact vehicle range (especially heating). In extremely cold weather, heating needs can decrease range up to 50%. Discuss options with your bus manufacturer if you are concerned about extreme cold.
Comparison to Conventional Buses: ESBs require much less maintenance than conventional buses. Without oil changes or after-treatment systems, fleets can expect to see a reduction in routine maintenance costs.
Best Practices: Ensure your bus manufacturer has local options to provide warranty repairs and possibly routine maintenance, if required. Incorporating service-level agreements within procurement documents is also advised.
Comparison to Conventional Buses:The engine or powertrain warranty in conventional buses will be replaced with a traction motor and high-voltage battery warranty for ESBs.
Typical Warranty Length:High-voltage batteries are now being covered for up to 10 years with options for extended warranties. Confirm with your manufacturer what options are available.
Step 2 - Charging Basics
Planning for and installing the correct charging infrastructure is just as important as selecting the correct ESB. Fleets must understand the components of charging infrastructure and what power levels are available. More information on charging infrastructure development is available on the Alternative Fuels Data Center.
The Electric School Bus Initiative (ESBI) produced a series of videos on the basics of charging infrastructure.
Power Source: Typically, power is delivered to the charging station through the grid (transmission) or an on-site power source (e.g., renewable generation)
- Electricity is properly managed through transformers, switchgears, and load centers.
- The power source should be connected to the charging equipment through a dedicated circuit correctly sized to the power requirements.
Charging Station: The charging station transfers power from the power source or grid to the bus. The station is made up of the unit itself, the cord, and the connector to the vehicle.
Measuring Power: Power is delivered from chargers to buses in kilowatts (kW). The higher the kW rating of the charger, the faster it will charge the vehicle.
Using Power and Time to Calculate Energy:
- Energy delivered to the bus battery (kWh) = charger power level (kW) x charging time (hours).
- Example: A 25 kW charger plugged into a bus for 4 hours will theoretically recharge 100 kWh of the bus battery (25 kW charger x 4 hours = 100 kWh). The total recharge will be somewhat less due to charging curves and electricity loss. More on calculating charger power will be discussed in Phase Two: Step 11.
AC Level 2 Charging (Level 2) vs. Direct Current Fast Charging (DCFC): ESBs can be charged by two different options at multiple power level (kW) options. The chart below details basics differences between the two.
Level 2 |
DCFC |
|
---|---|---|
Power Level |
3-19 kW |
15-350+ kW |
Power Requirements |
Compatible with Single or 3-phase power |
Usually requires 3-phase power. *Some low power DCFC units are compatible with single phase power |
Connector |
J1772 |
CCS1 |
ESB Compatibility |
Level 2 not an option on some ESB models |
DCFC offered on all ESB models |
Grid Infrastructure & Costs |
Lower power may reduce the need for infrastructure upgrades |
Higher power can increase infrastructure needs and energy costs through utility demand charges. |
Step 3 - Utility Basics
Utilities will be replacing traditional fuel providers, and they will also be the fleets’ partners when it comes to planning and installing charging infrastructure. Fleets must have a basic understanding of what makes up their electricity costs and how service is provided. Part 2 of the Flipping the Switch series, Working with Electric Utilities, provides some guidance on understanding utility essentials. Phase Two: Step 8 has more information about utility rates and engagement.
Electric Bill Components: Liquid fuel is usually sold by volume only, so the total cost is simply the volume used times the price per unit volume. In contrast, electricity charges from most utilities have three separate components.
- Consumption: Total energy consumed in kilowatt-hours ($/kWh). These are the standard charges all utility customers pay, including residences.
- Demand: Maximum power used at one time (also called “demand”) in kilowatts (kW). These are additional fees typical for commercial utility customers that can significantly affect bills when charging numerous buses at once.
- Fixed Fees
Managing Electricity Costs for ESBs: Generally, fleets can reduce costs by managing when and how fast they charge electric vehicles. More details on managed charging strategies can be found in Phase Three: Step 14.
Small ESB deployments or pilot projects may be able to utilize the existing utility service at a facility through spare breakers. Deployments with more than a few buses will typically require building a new electric service.
Building an Electric Service at a Facility (Typical)
- Electric utility installs power lines up to the property.
- Customer hires contractors to install equipment such as transformers, meters, and switch panels on the property
- Customer pays for all equipment and installation (some utilities may pay for and even install some equipment through programs that are discussed in Phase Two: Step 8)
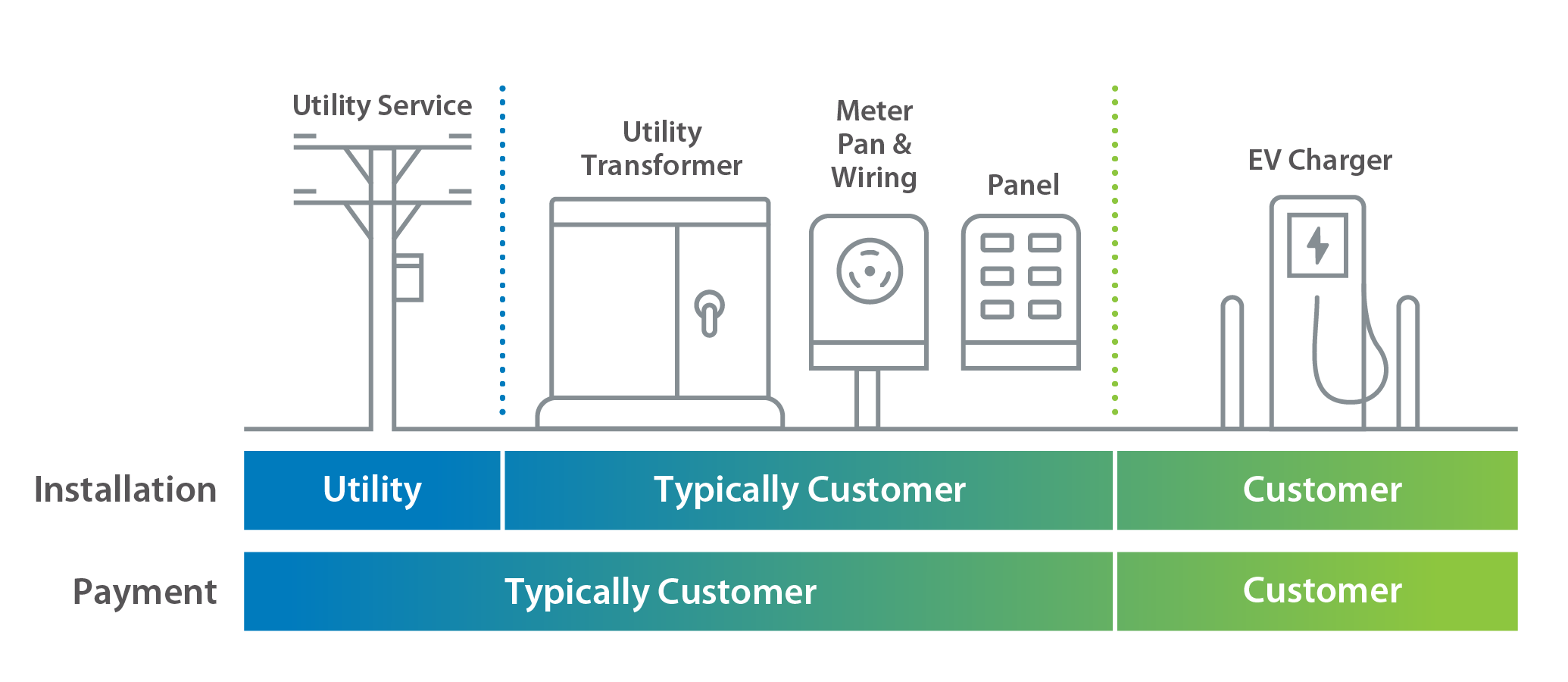
Components to bring electrical service to a charging site include service wire, transformers, meters, panels, and chargers. Who is responsible for payment and installation of each component varies by utility or incentive program, so talk with your utility early.
Step 4 - Gauge Support
Having the support of your organization, as well as the wider community, is an important element of transitioning to electric school buses. Listen to stakeholder groups and understand their concerns. Resources from this guide, such as this FAQ document from the Electric School Bus Initiative, can help address those concerns.
Best Practices: Ensure your board and leadership are aware of the benefits of bus electrification as well as the potential challenges. Ensure your board and leadership are supportive of incorporating ESBs into operations before moving forward with significant ESB efforts.
Resources:
- Watch a video from the Beneficial Electrification League that highlights why your fleet should consider deploying ESBs
- Read, “Why We Need to Transition to Electric School Buses” from the Electric School Bus Initiative details the benefits of transitioning to ESBs
- Provide opportunities to raise awareness among community members about the project.
- Share the benefits to students and cost savings to the fleet, especially through grants and incentives.
- Address community concerns with objective information.
- Talk with your contractor about what it will take to add ESBs to the fleet.
- Identify cost differences and be sure your contractor is aware of how ESBs will impact their operations (range, charging, maintenance, etc.).
- Listen to any concerns from bus drivers, maintenance technicians, and other district employees, especially around safety or job impacts.
- Address these concerns in your training and workforce development programs and ensure employees are aware their concerns were addressed. Further discussion of training is provided in Phase Four: Step 20 will go into more detail on types of training.
Step 5 - Define Goals
Common goals associated with ESB deployment include:
Start small: A test pilot of 10 or fewer buses may provide you with the experience and lessons learned to feel comfortable with further fleet electrification while minimizing risks. A test pilot of this size can often be supported with reasonable levels of infrastructure.
Assign ESBs to shorter routes with minimal mid-day or afterschool activities to address initial range concerns from drivers.
Focus initial pilots on drivers who want to drive ESBs: By having a positive experience, they can communicate the benefits of ESBs with other drivers.
Track your data, including bus efficiency, range, charger downtime, etc. to help you identify and resolve issues and inform subsequent procurements.
Talk to peer fleets: Learn from others who have adopted ESBs. Utilize the Electric School Bus Forum to connect with ESB fleets.
Many cities and states are now mandating that school districts adopt ESBs. If you do not know if you are subject to an ESB mandate, check with your state or local energy and/or environmental department.
If you are attempting to meet a mandate to transition to ESBs, ensure that your plan addresses the long-term turnover of your fleet. A crucial element to this will be coordinating with your utility early about the power needs for full fleet electrification.
Resources for ESB policies include:
- The federal and state ESB laws compiled on the AFDC Laws & Incentives Page
- The ESBI State Legislative Tracker that follows ESB state legislation
- The Center for Climate and Energy Solutions that maintains a Policy and Incentive Map.
- ESBs can be an ideal way for school bus fleets to meet emissions reduction goals. They produce zero tailpipe emissions, reducing localized pollutants from diesel exhaust that are harmful to the health of students and people living in the communities where the buses operate.
- Phase Two: Step 11 contains information on Argonne National Laboratory’s Alternative Fuel Life-Cycle Environmental and Economic Transportation (AFLEET) Total Cost of Ownership Calculator and the Fleet Procurement Analysis Tool from the Electric School Bus Initiative. Both resources include emission reduction results in their analysis.
- Reduced maintenance and fuel costs are two potential benefits of ESBs compared to conventional buses.
- Unprecedented sources of funding are currently available for ESBs and associated charging infrastructure. Taking advantage of these opportunities can help fleets realize lower total costs for ESBs over conventional buses.
- Phase Two: Step 10 and Phase Two: Step 11 will review how to identify funding and perform a cost analysis.
Step 6 - Identify Team
Bus fleet electrification relies on strong collaboration and partnerships with stakeholders who have clearly defined roles and responsibilities. In your organization, these roles may be separate as listed below or combined depending on your organization’s size and staffing.
ESB Champion—typically the fleet manager
- Determine the buses and routes suitable for electrification
- Determine the number, type, and locations of charging stations
- Identify external funding sources
- Assemble and coordinate stakeholders and responsibilities
- Manage the electrification transition
Facility Manager
- Assist with determining charging station locations
- Coordinate facility and grid infrastructure assessments and upgrades
Procurement Manager
- Coordinate external funding applications
- Identify and finalize procurement methods for buses and charging stations
Drivers/Operators
- Understand efficient operation of electric school buses
Maintenance Staff
- Understand high-voltage safety and ESB maintenance
You may want to explore partnering with a business that owns, installs, operates, and/or maintains charging systems and/or ESBs on your behalf, sometimes called electric-as-a-service. These businesses can:
- Secure funding
- Access additional tax credits
- Reduce upfront costs through leasing or providing an as-a-service business model
- Avoid the learning curve and time investment for ESB charging by offering turnkey services
- Stabilize operating costs.
To learn more about business partnership options, see the ESBI’s Business Models Guide and Electric-as-a-Service Directory.
If your fleet decides to go this route, numerous providers have been awarded cooperative contracts through Sourcewell under their Electric Vehicle Equipment category.
Learn Resources
- Alternative Fuels Data Center’s (AFDC) Flipping the Switch: Electric School Bus Introduction – Video series with information on the basics of adopting ESBs
- AFDC’s Developing Infrastructure to Charge Electric Vehicles – Basics on charging stations
- Electric School Bus Initiative’s (ESBI) All About Charging Infrastructure – Video guides on the components of charging infrastructure from World Resources Institute’s Electric School Bus Initiative
- AFDC’s Flipping the Switch: Working with Electric Utilities – Video series with basics of working with utilities
- ESBI's Frequently Asked Question – Document that can answer many of the initial questions raised during the electrification process
- Beneficial Electrification League’s Electric School Bus Initiative – Video about why an electric school bus is a better option for schools
- ESBI’s Why We Need to Transition to Electric School Buses – Article on the benefits of school bus electrification
- Joint Office of Energy and Transportation’s Electric School Bus Forum – Online forum for school bus operators to connect with one another
- AFDC’s Laws & Incentives Search – Searchable database of laws and incentives available across the United States
- ESBI’s State Legislative Tracker – Database tracking ESB state legislation
- Center for Climate and Energy Solutions’ U.S. State Clean Vehicle Policies and Incentive Map – Database tracking state clean vehicle policies and incentives
- Argonne National Laboratory’s Alternative Fuel Life-Cycle Environmental and Economic Transportation (AFLEET) Total Cost of Ownership Calculator - Online total cost of ownership and emissions calculator for electric school buses
- ESBI’s Fleet Procurement Analysis Tool – Online total cost of ownership calculator for electric school buses from the Electric School Bus Initiative
- ESBI’s Electric School Bus Business Models Guide – Resource to help fleets identify the appropriate business model to support electrification of school buses
- ESBI’s Electric-as-a-Service Directory – Directory of firms that offer services to aid school fleets in bus electrification
- Sourcewell’s Electric Vehicle Equipment – Resource for ESB partner cooperative contracts.
Phase Two: Scope
Overview: Scope
This phase contains steps to conduct a preliminary bus electrification assessment with the goal of identifying some of the major elements of your project. During this phase you will:
- Define which routes can be electrified and where buses will charge
- Hold an initial discussion with your utility
- Identify funding sources and estimate costs
- Establish buy-in for your project.
Step 7 - Fleet Assessment
Before moving forward, determine if you have routes that can be serviced by electric school buses (ESBs) and where those buses will charge. Start with conducting high-level assessments to ensure your routes and facilities will be compatible with bus electrification. Then, if they are, you will refine your route and site analyses as you move through this planning guide.
Consider the typical lowest temperatures in your area and the total miles covered by each bus assignment on a typical day. Use the graphic below to conduct a basic feasibility screening. You might be able to quickly identify some routes with lower daily mileage where switching to ESBs would be straightforward. Operating ESBs on longer routes or in cold weather will require additional planning (information on this will be covered later in the planning guide).
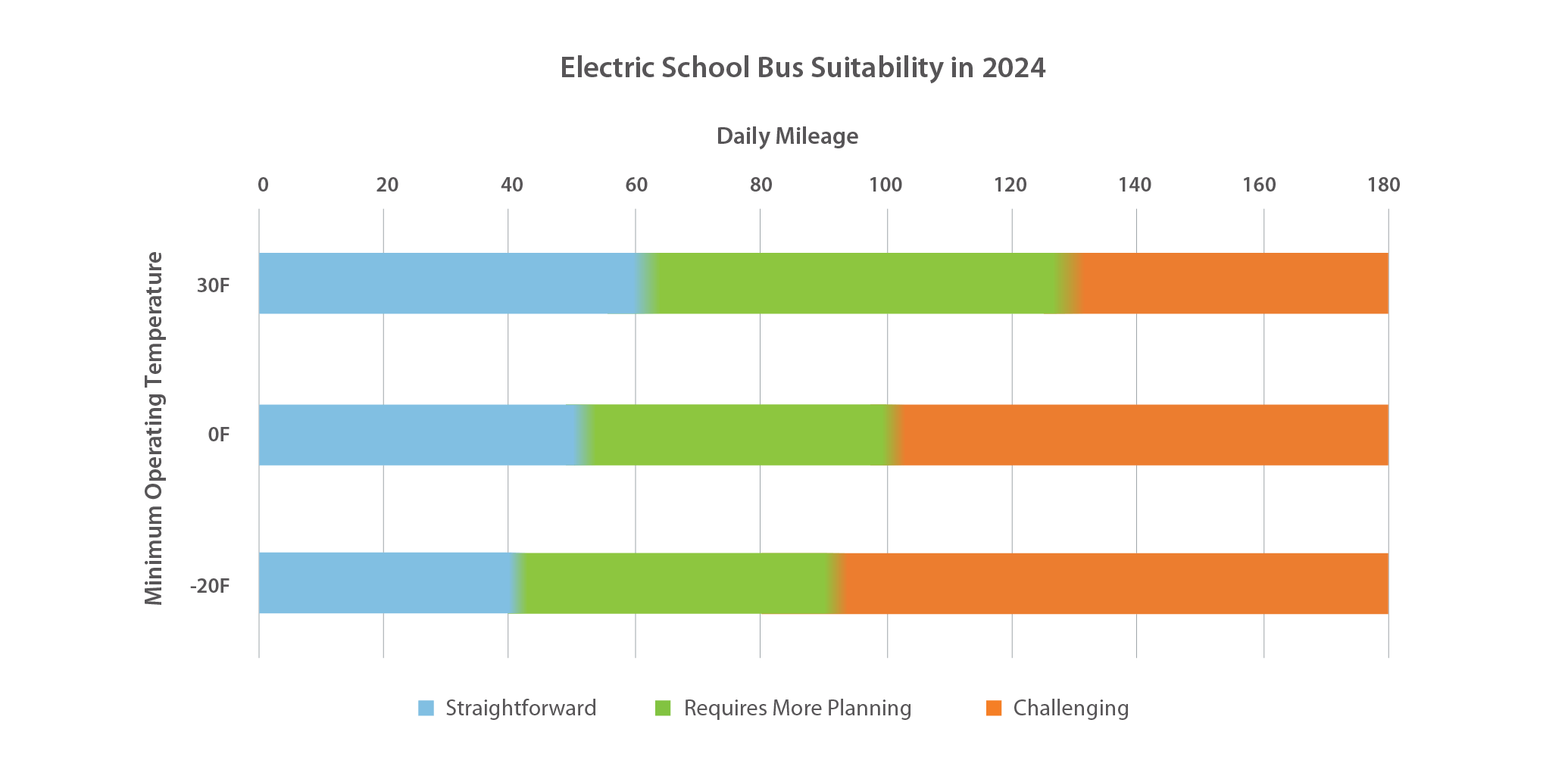
This chart illustrates how daily mileage and minimum operating temperature impacts electric school bus suitability. Situations that are straightforward may be able to use lower powered chargers and forgo mid-day charging. As routes move into the “Require More Planning” and “Challenging” levels, fleets will need to incorporate higher powered chargers and larger bus batteries. Fast charging during dwell periods also might be needed.
It is best to install charging stations where buses park mid-day and overnight. If possible, an initial small deployment may be able to locate chargers at facilities with sufficient existing load capacity so that new grid infrastructure is not required.
While you are identifying potential charger sites, keep in mind the following considerations to save costs:
- Stay close to electric panels or transformers to minimize lengths of conduit and wiring
- Minimize difficult or lengthy trenching under paved surfaces
- Utilize walls where chargers or conduit can be installed.
Step 8 - Engage Utility
With this preliminary information about a potential ESB project, you are ready to have an initial discussion with your utility. If you need assistance finding your utility point of contact, email cleanschoolbusta@nrel.gov.
Discuss the following questions with your utility. They will require some basic information at this point about your sites and buses. Remember this is merely a scoping discussion, and you will come back to your utility later in this process to further define your needs.
- Utility rates can be comprised of multiple elements. See Part 2: Working with Electric Utilities of the Flipping the Switch series for a discussion on rate structures. Some of the most common rates are:
- Energy Rate—Your base rate charged in $/kWh. In the United States, it typically ranges from $0.03–$0.14.
- Demand Charge—A rate paid in $/kW by many commercial users for the maximum kW usage for a certain period of the month. If you are subject to demand charges, minimizing charger power levels or incorporating managed charging will be essential.
- Time-of-Use (TOU) Rates—These rates fluctuate depending on the time of day, often called on-peak or off-peak hours. Typically, charging will be less expensive in the evening, and managed charging can help fleets take advantage of these rates.
- Find out about any special electric vehicle rates that might be available and any usage requirements for special rates.
- Ask your utility how much it will cost to charge and at what times of the day you should be charging.
Many utilities offer incentives, rebates, make-ready programs, and/or onsite assistance to customers electrifying their fleets.
You may be able to identify what is available by consulting the U-Finder tool from the Joint Office of Energy and Transportation or Electric Vehicle Make-Ready Programs Guide from the Electric School Bus Initiative (ESBI), which explains core components and benefits of these programs and includes a table of make-ready programs available throughout the country.
- Use the chart below to estimate the total power you will need from your utility to charge the number of ESBs you plan to purchase in your initial procurement phase. (This is a high-level planning estimate. You will refine these numbers during Phase Two: Step 11.
- For the routes you expect to electrify, take the point on the graph where the daily mileage meets the minimum temperature in your area. The values inside the graph will then indicate your power requirement (kW per Bus).
- Example: A bus that will travel 80 miles per day at a minimum of 0° F is estimated to require a 25kW charger.
- Share this estimate with your utility. Ask if they can reasonably supply that amount of power and what potential infrastructure upgrades may be needed.
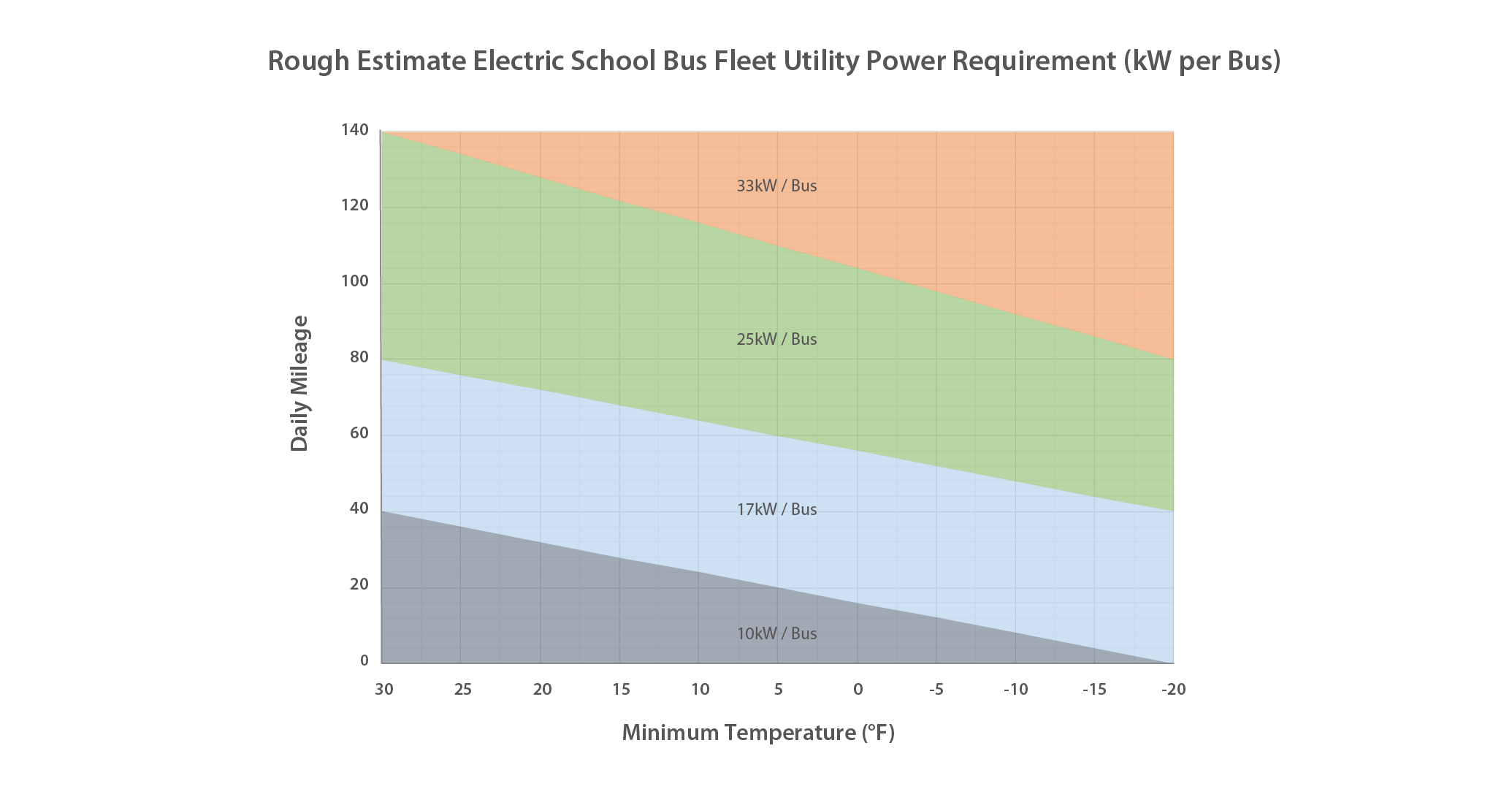
This graph shows an average charger power level required per bus at different daily mileage and minimum expected temperatures. Use this graph to provide your utility with a high-level estimate of power needs onsite during initial discussions.
- Discuss your anticipated long-term ESB procurement plans with your utility (e.g., 50% of your fleet will be ESBs in 5 years or 100% ESBs by 2030) to determine potential infrastructure upgrade needs and timing. Large electrification projects typically require new grid infrastructure, which can be costly and require long lead times (3–5 years or longer).
- Your utility may need more information than you have at this point, but it is good to get these plans into your discussion and make the utility aware of your intentions for fleet electrification.
- Ask your utility about other considerations that might impact your plans. These could include requirements for new services like security deposits or easements, application processes, or any other advice they have.
Step 9 - Identify ESBs
Consider your standard safety, sizing, and other specification requirements and determine what ESB models on the market can meet your criteria. ESBs are available in types A, C, and D with numerous configurations and options.
Online resources include School Transportation News' Buyer's Guide 2024; the ESBI’s U.S. Buyer's Guide; CALSTART’s Zero-Emission Technology Inventory tool, which allows comparison of ESB models; and the Alternative Fuels Data Center Advanced Vehicle Search Tool.
Once you identify ESB models that meet your required specifications, talk with dealers and/or manufacturers to ensure they have local service and parts support and that all warranties meet your requirements, including the high-voltage battery warranty. Pay attention to all-electric options such as battery size, range, charging compatibility (e.g., some ESBs are not compatible with Level 2 charging), and HVAC options, including auxiliary heaters in cold climates. You will do more work in the planning phase to determine your exact needs regarding these components.
You can also consider repowers, which involve replacing conventional powertrains with all-electric versions. This may be a good option for fleets with existing buses with chassis and bodies that are in good condition but are up for replacement. For more information about repowers, see the Repower Explainer from World Resources Institute.
Step 10 - Identify Funding
Grants, rebates, and other funding mechanisms can provide funding to purchase ESBs, charging infrastructure, or sometimes both. Some fleets may also opt to enter into business partnerships with third parties that offer funding for up-front electrification costs.
There is unprecedented funding available at this time for ESBs and charging infrastructure. Taking advantage of these funding opportunities will often make your electrification projects on par or less expensive than opting for conventional buses. Resources to identify funding include:
- The U.S. Environmental Protection Agency’s Clean School Bus Program provides $5 billion in federal funds over 5 years (2022–2026) for ESB deployment
- Search the U.S. Department of Energy’s Alternative Fuels Data Center for school bus on the Laws and Incentives page
- Download Clearinghouse: Electric School Bus Funding and Financing Opportunities from the ESBI
- Search the Database of State Incentives for Renewables and Efficiency from the N.C. Clean Energy Technology Center
Tax-exempt entities like school districts are also now eligible for IRS tax credits up to $40,000 per bus and for qualified charging infrastructure. A fact sheet on New Tax Credits and Direct Payment for School Districts from the Alliance for Electric School Buses outlines the process for school districts.
Use the U-Finder tool to identify programs and incentives offered by electric utilities for charging infrastructure, advantageous electricity rates, or ESB purchases.
As discussed in Phase One: Step 6, fleets can consider partnering with a business that owns, installs, operates, and/or maintains charging systems and/or ESBs on your behalf, sometimes called electric-as-a-service. To learn more about business partnership options, see the World Resources Institute’s information on these business models and directory of providers. If your fleet decides to go this route, numerous providers have been awarded cooperative contracts through Sourcewell under their Electric Vehicle Equipment category.
Step 11 - Analyze Cost
This step will help you estimate the costs associated with acquisition and operation of ESBs and compare those costs to available funding sources. This is a high-level estimation of your potential costs that should help inform your decision to move forward.
Before deciding whether to seek funding, roughly estimate your ESB costs. Your dealer may provide pricing or pricing may be available from a cooperative purchasing agreement or other mechanism. Below are some numbers to begin a rough estimation:
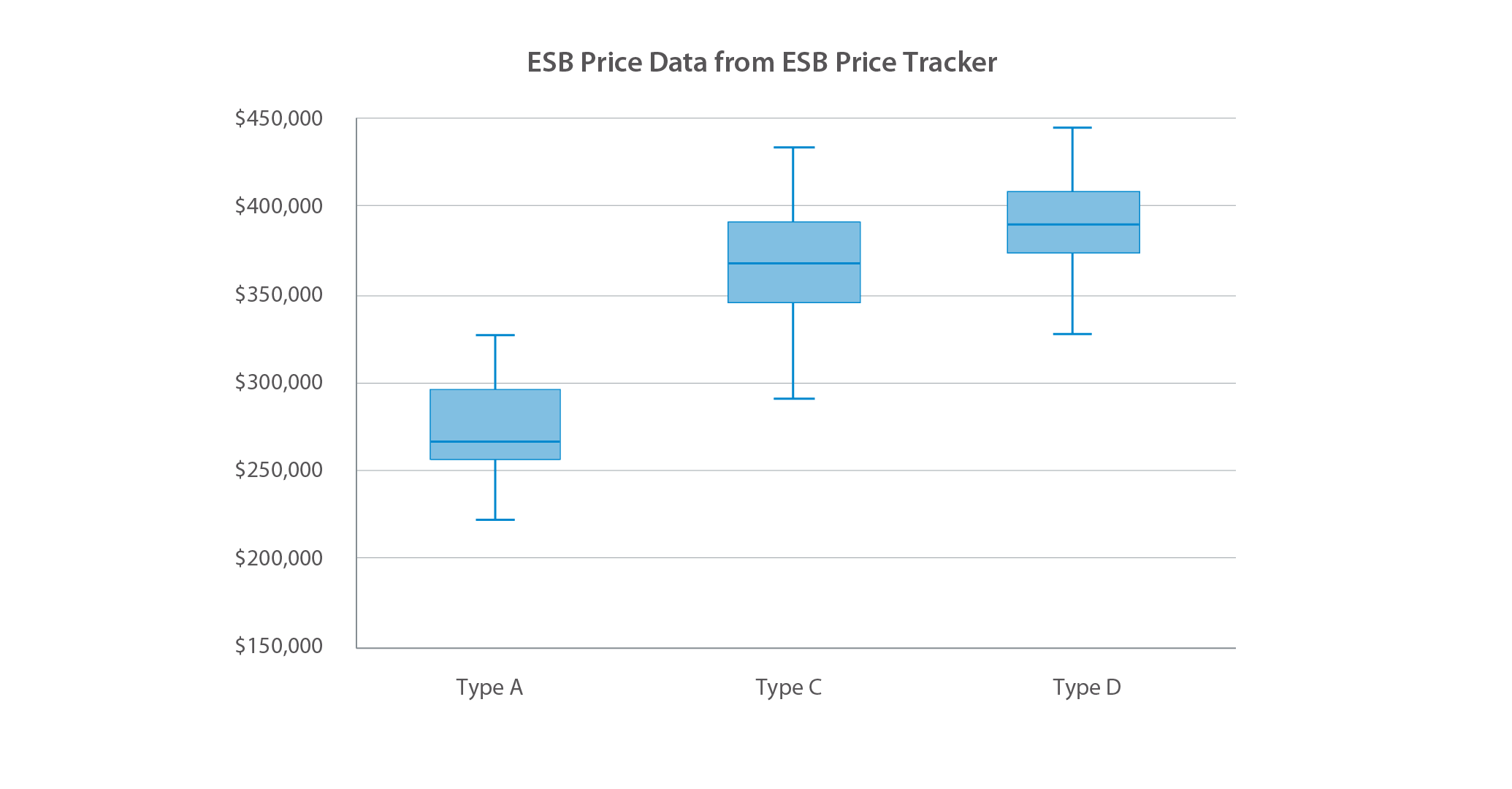
This chart shows the range of electric school bus prices, including the median represented by the line in the boxes, upper and lower quartiles represented by the boxes, and upper and lower extremes represented by the whisker lines (i.e., the lines extending above and below the boxes). Prices are based on data from the World Resources Institute’s Electric School Bus Price Tracker, which provides recent contract prices for electric school buses across the country.
Estimating your charging station costs can be difficult due to numerous charger configurations and nearly infinite variables around installation. In this preliminary analysis step, use the chart below to estimate charging depot costs based on the power levels you identified in Phase One: Step 6. If you predict a simple installation based on your site factors (minimal or no trenching, short conduit runs, etc.) use the lower range of the displayed estimates. If you predict difficult site factors, opt for the higher range.
Note that capital costs vary widely. Some projects may see final costs outside of the range in this chart due to features that are unavoidable. Additionally, the same or other projects may have elements that produce important operating cost savings that outweigh higher upfront costs.
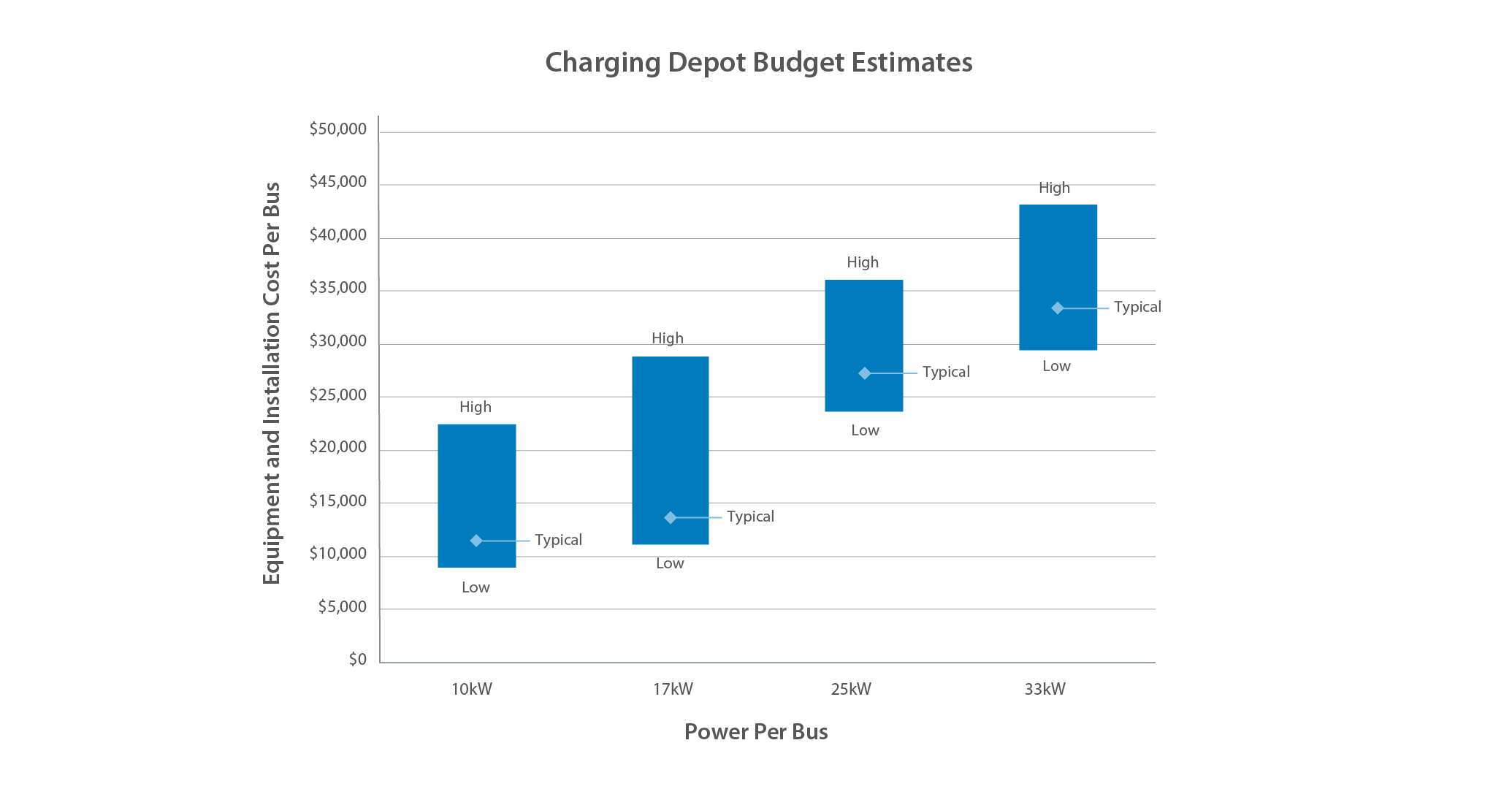
This chart shows estimated costs for charging stations by power level based on nationally available pricing. Cost estimates include both equipment and installation.
Charging Equipment
Charging equipment costs vary based on charging level, mounting type, ports per charger, and other options. Level 2 chargers are much less costly, but DC fast chargers are more likely to be compatible with all bus models and come in a wider range of power levels. Wall-mounted chargers and dual-port chargers without cord management systems or connectivity tend to be the least costly to purchase. Local ESB fleets are a great resource for cost estimates if they are willing to share that information.
Equipment Installation
Installation costs vary widely and are highly location specific. The lowest-cost installations have overhead utility service nearby, minimal trenching requirements, and wall-mounted chargers.
While upfront costs are currently much greater for electric buses than for conventional buses, many bus fleets may achieve a lower total cost of ownership over the lifetime of an electric bus, particularly if grant, rebate, or other outside funding reduces upfront costs. Some fleets may wish to calculate the total cost of ownership savings offered by electric buses to help establish buy-in.
Operating Costs
Operating costs, such as fuel and vehicle maintenance, are typically lower for ESBs than diesel school buses. Ask local ESB fleets about their experiences with operational cost savings.
Costs associated with the charging infrastructure vary but include software subscriptions, station management, preventative maintenance, and corrective maintenance. Charging station operators generally use 10% of the up-front cost to estimate annual station maintenance. For example, an owner that pays $20,000 to purchase and install a charging station may want to assume they will need 10%, or $2,000 per year, for maintenance.
Total Cost of Ownership Analysis
A total cost of ownership (TCO) analysis can help determine how operating cost savings could potentially offset the up-front capital costs associated with purchasing ESBs and charging infrastructure. If you are interested in conducting a TCO analysis estimate with the information you have at this point, the Alternative Fuel Life-Cycle Environmental and Economic Transportation (AFLEET) TCO Calculator accepts custom inputs and contains maintenance cost assumptions from Argonne National Laboratory studies.
For a more detailed TCO analysis, you can utilize the Fleet Procurement Analysis Tool from ESBI, which also includes elements such as infrastructure cost and utility rate structures. Since you may not yet have a lot of detailed data, this in-depth analysis may be best left until later in the process.
These tools can also provide estimates of potential emissions reductions.
Step 12 - Scope Project
At this point, you are ready to make an informed decision about whether to move forward with fleet electrification and establish a scope for your project. This process may require you to re-evaluate and re-scope after receiving feedback or seeing results.
Keep your initial electrification projects simple when possible. Focus on shorter routes, install lower power charging, and take advice from fleets that are successful with bus electrification.
- Take advantage of the unprecedented funding currently available for fleet electrification.
- Maintain consistent and open communication with your utility. Rates, programs, and incentives are always evolving, and any changes could alter the outcomes of your plan.
Using information learned during this phase, you should have the following items defined for your project:
- The number of ESBs you plan to procure, what routes they can be placed on, and what makes/models can meet your existing specifications
- Where you plan to charge your buses and confirmation from the utility that they can supply the estimated power needs
- Utility rates and how they may affect charging costs or times
- What external funding you will seek and high-level cost estimates for your buses and charging infrastructure.
- Optional elements:
- Long-term electrification plans and support from your utility
- Total cost of ownership analysis on your expected costs or savings from electrifying your fleet
- Expected emissions reductions benefits of electrification
- Potential partnerships with an electric-as-a-service provider.
ESBI's technical partner VEIC developed a template pitch deck that can be customized to help present the costs and benefits of bus electrification.
Scope Resources
- Alternative Fuels Data Center’s (AFDC) Flipping the Switch Part 2: Working with Electric Utilities - Video series with information on basic utility rate structures for ESBs
- Joint Office of Energy Transportation’s U-Finder — Tool for identifying utilities and incentives
- Electric School Bus Initiative’s (ESBI) EV Make-Ready Programs Guide - Guide from the ESBI that explains core components and benefits of utility programs and includes a table of make-ready programs available throughout the country
- School Transportation News Buyer's Guide 2024 — Catalog of available ESBs with specs and options
- ESBI’s U.S. Buyer's Guide — Catalog that presents ESB models and detailed specifications
- CALSTART’s Zero-Emission Technology Inventory Tool — Interactive online resource to identify and compare available ESB models
- AFDC’s Advanced Vehicle Search Tool — Searchable online database of available ESB models
- ESBI’s Repower Explainer — Article of eight essential things to know about ESB repowers.
- U.S. Environmental Protection Agency’s Clean School Bus Program — Provides $5 billion over 5 years (2022–2026) to replace existing school buses with zero and low-emission models
- AFDC's Laws & Incentives Page — Searchable database of laws and incentives available across the United States
- ESBI’s Clearinghouse: Electric School Bus Funding and Financing Opportunities — Spreadsheet cataloging ESB funding sources
- N.C. Clean Energy Technology Center's Database of State Incentives for Renewables and Efficiency — Database of policies and incentives by state
- Alliance for Electric School Buses’ fact sheet on tax credits and elective payments — Resource outlining the tax credit process for school districts
- Joint Office of Energy Transportation’s U-Finder — Tool for identifying utilities and incentives
- ESBI's Electric School Bus Business Models Guide — Resource to help fleets identify the appropriate business model to support electrification of buses
- ESBI's Electric-as-a-Service Directory — Directory of firms that offer services to aid fleets in bus electrification
- Sourcewell's Electric Vehicle Equipment — Resource for ESB partner cooperative contracts
- World Resources Institute’s Electric School Bus Price Tracker — Resource tracking ESB prices across the country
- Argonne National Laboratory’s AFLEET TCO Calculator — Online total cost of ownership calculator
- ESBI’s Fleet Procurement Analysis Tool — In depth, spreadsheet-based total cost of ownership calculator
- ESBI/VEIC template pitch deck — Customizable slides to relay the benefits of electrification
Phase Three: Plan
Overview: Plan
The information in this phase will help you balance all the options and create the most efficient and cost-effective plan to meet your fleet’s needs.
During this phase you will:
- Identify specific routes, buses, and chargers that meet student transportation requirements
- Design your charging infrastructure and decide whether to incorporate charge management or other advanced charging methods
- Complete all site planning and onsite coordination with your utility
- Issue requests for proposals or enter into contracts for your buses and chargers.
Some fleets may be interested in external assistance during this phase. The Clean Bus Planning Awards program funded by the Joint Office of Energy and Transportation provides free technical assistance to eligible fleets to create bus electrification plans, including a detailed route analysis. This technical assistance is available through fiscal year 2024, which ends September 30, 2024. Many states and utilities also offer fleet electric transition planning opportunities. Identify these opportunities by using the U-Finder tool on the Alternative Fuels Data Center or by searching utility or state energy office websites.
Step 13 - Route Analysis
A detailed route analysis should evaluate route distances, dwell times, external temperatures, charging strategies, and battery parameters. This analysis should be done using assumptions about the least efficient operating conditions for the buses to prepare for days with poor weather conditions, inefficient driving, etc. The results will help you determine what bus configurations will work for your routes by providing information on energy usage by route, optimal bus battery sizes, and recommended charger power levels. A recording of the Fleet Planning and Route Analysis webinar from the U.S. Environmental Protection Agency’s (EPA) Clean School Bus Program provides more details on how to conduct a route analysis.
The Joint Office of Energy and Transportation developed the Electric School Bus (ESB) Route Analysis Tool to help you conduct your route analysis. Watch an instructional video for guidance on using the tool.
This tool will provide you with information on what buses and chargers will be compatible with your specific routes. You can use the tool outputs to better understand the recommendations you will receive from bus dealers or manufacturers, charging station providers, and local ESB fleets.
Results
- Buses
- Bus efficiency (kWh/mile) and battery size (kWh) can vary greatly between makes and models. These two factors will determine whether a bus is compatible with a specific route, as together these factors establish overall driving range.
- Your route analysis should indicate what bus models are compatible with each of your routes and the optimal battery size if the manufacturer offers multiple battery sizes.
- Chargers
- Your route analysis should indicate what size (kW) chargers will enable route completion on least efficient days.
- It is important to right-size charging stations. Over-sizing power outputs can increase up-front costs and grid impacts. Under-sizing power outputs could prevent ESBs from fully charging and being able to complete routes.
Step 14 - Charging Considerations
Evaluating your charging options begins with the three considerations below. At the very least districts need to ensure that their buses and chargers are compatible or interoperable with one another. Most districts will also want to consider some form of advanced charging like networked chargers or managed charging.
It is essential to choose chargers that are interoperable with your ESBs, meaning the buses and chargers can work and communicate with one another. Not all buses and chargers are interoperable, and failure to acquire interoperable equipment can result in the inability to charge buses. Interoperability depends on both bus and charger software and hardware. Ask your bus and charger providers for a list of vehicles and the chargers they are compatible with. You also might consider requiring interoperability in contracts or seeking out a managed charging provider that will ensure interoperability in their services. See the Charging Management Partners section below for more information on what you should look for in these providers.
Fleets that are very small or are not subject to demand charges can use relatively simple charging plans. A one-to-one bus-to-charger ratio where individual chargers are installed at each parking space and charging begins once the bus is plugged in will serve the charging needs for these fleets.
Larger fleets and those subject to demand charges will want to consider networked and/or managed charging, which will add complexity to a project but may provide significant cost savings.
Networked Charging
Charging stations can be connected to a data network and software. This typically requires a monthly fee per charger. Advantages of networked charging include:
- Real-time monitoring (e.g., errors, charger status) to ensure uptime
- Data reporting (e.g., charging sessions, utilization, energy consumption, energy costs) to inform fleet operations
- Managed charging to address electrical capacity or demand charge issues.
Managed Charging
Managed charging is scheduling charging times and/or reducing charging power levels while ensuring vehicles are always charged and ready when needed.
- Manage Charging Power
- Why: Fleets can be subject to demand charges that may drastically increase electricity costs.
- How: Chargers are usually sized to fully charge a bus based on the energy use for its least efficient day. On other days, there will be extra charging capacity. Software and hardware help control this capacity to reduce utility bills.
- Manage Charging Times
- Why: On some electric rate plans, electricity is much more expensive during certain hours of the day.
- How: A managed charging system can allow a bus driver to plug in at the end of a shift but use software to delay the start of charging until later when energy is less costly.
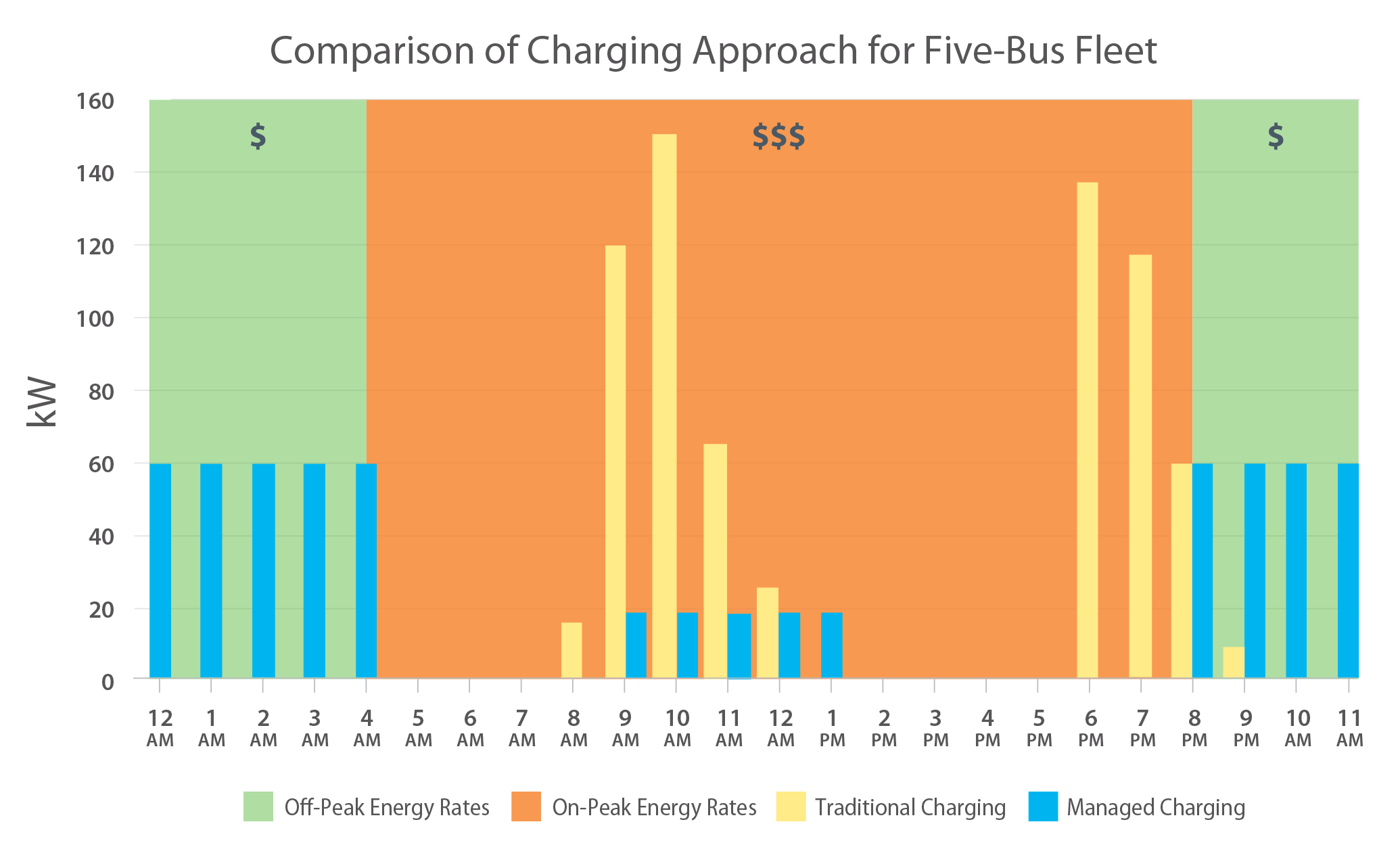
This graph shows an example of how managed charging can shift charging power and time to reduce demand (total kW) and delay charging times when rates can be lower.
To learn more about managed charging, read Not Just Smart: The Importance of Managed Charging from CALSTART.
Managed charging is different from bidirectional (vehicle-to-grid) charging, which is a more advanced topic. If your utility will offer a program to compensate for bidirectional charging, more information is available in Phase Five: Step 25.
If you are interested in networked or managed charging, you will need to select a vendor or business partner who will provide the service and software, and possibly the chargers as well. See the Charge Management Software Catalog from the Electric School Bus Initiative (ESBI) or review the World Resources Institute’s directory of providers (for more information, see the Electric Fleet Business Partnerships section of Phase Two: Step 10). As always, talk with local fleets to gain insights from their experiences with charging providers.
A charging provider should offer:
- Flexibility and proof of interoperability between multiple bus and charger manufacturers.
- The ability to manage vehicles, chargers, and utilities. They should be a one stop shop for all your charging needs or issues.
- The ability to maintain the handshake between the bus and charger without requiring onsite support.
- An easy-to-use user interface and any needed training on that interface.
- A customizable alert system for charger health, faults, and other items.
- Options for remote monitoring and diagnosis.
- Vehicle-to-grid capabilities, if desired.
The Incorporating Charge Management, Solar, Battery Storage, and Bidirectional Charging webinar from the EPA’s Clean School Bus Program provides more information on selecting a charge management provider.
Step 15 - Utility Check-In
At this point, you should check in with your utility and confirm information from previous discussions or provide updates if your plans changed. During the discussion with the utility, you should:
- Let the utility know the number and size of the chargers you are planning to install based on the results of your route analysis. Confirm if you will need a new service.
- Ask the utility if they provide onsite assessment services for customers. They may be able to help you identify optimal locations to place your charging infrastructure and save costs.
- Discuss any utility incentives or make-ready options that are available to your fleet.
- Some utilities have programs where they will pay for required upgrades or install and own charging infrastructure in exchange for a premium on your monthly bill. See examples in the ESBI Electric Vehicle Make-Ready Programs Guide.
- Smaller utilities may also be willing to listen to proposals that are mutually beneficial. Don’t hesitate to ask about incorporating new ideas or programs that are working for other utilities.
If a new service is required, you will need to follow established processes. Most utilities will not proceed further until you complete a new service request and submit engineering plans, which will require you to have your EV charging infrastructure contract in place. Options for charging infrastructure procurement are discussed in Step 17 of this phase.
Step 16 - Infrastructure Design
In Phase Two: Step 6, you identified potential locations where your buses could charge. Now you will refine your charging infrastructure plans to incorporate your additional findings from these planning activities.
As you proceed with this step, you might find it challenging to weigh the costs and benefits of all the options. A business partner can help you navigate those considerations. If you do not already have a business partner, see Phase Three: Step 17 of this phase for potential vendors and methods to partner with them. This step can help inform the scope of work for your charging business partner or contractor. If you are planning without the help of a business partner, the ESB Facility Assessment Guide from VEIC contains in-depth processes to assess your facility and site your charging infrastructure.
There is no specific formula for creating the optimal site design. Below are the major items you will want to consider.
- Initial Site Layout
- Where is it easiest and least expensive to deploy your initial chargers?
- Are you limited by parking (pull-in/back-out) and do you need to require front or rear charging receptacles on your buses?
- Do you have space for chargers and bollards in and around parking spaces?
- Equipment Needs
- How many chargers and what kW and power level will you install?
- Have your confirmed interoperability between your buses and chargers?
- What mounting options and cable management do you require?
- Futureproofing
- Where will future ESBs charge?
- Is it cost effective to install conduit and stub ups during the initial installation?
- If you need a new service in the future, how will that be incorporated into site plans?
- How quickly will a new service be required and what are the costs and timelines?
- Network and Charge Management
- Do you require networked equipment?
- What elements of charge management do you require (see Phase Three: Step 14 of this phase)?
- Do you require remote monitoring of equipment?
- Do you require customized and/or real-time usage reporting?
- Training
- Do you require training on charger operation and maintenance?
- Maintenance
- Do you require a maintenance agreement with specific service level agreements, including response times?
- Are there regular maintenance procedures and if so, who will perform them?
Step 17 - Procurement
You are now ready to begin the procurement process for your ESBs and charging infrastructure. Depending on what method you choose, these could be separate or combined procurements. Either way, they will be highly dependent on one another and need to be done concurrently.
The three major points you should keep in mind are:
- Ensure you understand the complete costs for charging infrastructure before committing to bus procurement. At this point you have estimated infrastructure costs and you do not want to be surprised by additional costs after you have committed funds for an ESB.
- Ensure your bus model and chargers are compatible. This means the bus can receive the power level of the charger and it is interoperable, which can be confirmed by the charger manufacturer, bus manufacturer, or third-party software provider if you choose to utilize one.
- Ensure you understand your full timeline for charger acquisition and installation. This includes any required utility upgrades. Your chargers will need to be operational before deploying ESBs.
Services to own, install, operate, and/or maintain charging infrastructure and/or ESBs on behalf of a fleet can streamline procurement, as well as all other aspects of school bus electrification, including planning, utility engagement, maintenance, and training. They typically come with multiyear agreements that roll all services into one monthly cost. For more information on these business models, see Phase One: Step 6 and Phase Two: Step 10.
To learn more about business partnership options, see the World Resources Institute’s information on these business models and directory of providers.
If your fleet decides to go this route, numerous providers have been awarded cooperative contracts through Sourcewell under their Electric Vehicle Equipment category.
School districts have multiple options for purchasing ESBs. Many state contracts and national collaboratives such as Sourcewell or the Climate Mayors Electric Vehicle Purchasing Collaborative have multiple ESB models available. If your district opts to create its own request for proposals (RFP), you may be able to utilize this RFP template from the ESBI. Regardless of your procurement method, ensure your ESB specifications meet your state requirements.
Before deciding on a specific ESB model, talk with local ESB fleets to find out what options may be best for your fleet and if they have any lessons learned. If you need help identifying or contacting ESB fleets, contact the Joint Office of Energy and Transportation at cleanschoolbusTA@nrel.gov or reach out to your local Clean Cities and Communities coalition. Regardless of your method of procurement, pay special attention to the items below:
- Battery Size/Range: Your route analysis in Phase Three: Step 13 should have indicated what battery size will work for the routes you plan to electrify. Under sizing the battery may not allow you to complete routes at the bus’s end of life or during least efficient driving days. Oversizing your bus battery can add significant cost to the bus purchase price.
- Charging Station Power Levels: If you determined Level 2 charging is best for your fleet, ensure the bus model you select is compatible with Level 2 charging. All available ESB models will accept DC fast charging, but you need to ensure your bus accepts the maximum kW power you are planning.
- Heating, Ventilation, and Air Conditioning: Understand the different heating and cooling options available on different bus models. In addition to the input from your route analysis, talk with ESB fleets in similar climates and see what is working for them. For additional information on operating ESBs in hot and cold weather, see the Hot Weather Impacts on Electric School Buses and Cold Weather Impacts on Electric School Buses.
- Maintenance and Support: Ask your manufacturer or dealer about local warranty and regular maintenance and repair service. Not all local service providers are certified or prepared to work on ESBs, and shipping buses long distances for repairs can add to down time. If possible, incorporate service level agreements in procurement documents.
- Warranties: Consider extended warranties. The high-voltage battery and traction motors on ESBs are expensive and many other parts can be more expensive than their conventional counterparts since ESBs are a new and evolving technology.
- Training: Include training requirements from your manufacturer in your procurement documents. Phase Four: Step 20 will go into more detail on types of training. If you plan to create an RFP, see the Providing Training for Zero Emission Buses guide from the International Transportation Learning Center for recommended training language.
Selecting a charger model, size, and provider will depend on the ESB make and model you procure. You will need to determine the best way to procure the correct chargers and have them installed and operational before your buses arrive.
If your fleet elects to procure charging infrastructure and related services on a site-by-site or annual basis, be sure contracts include all the considerations listed in Phase Three: Step 14. of this phase. See the ESB and Charger Procurement RFP Template from ESBI for example language. You may also want to reference the Vetted Product List, which provides a list of charging equipment technical specifications vetted by the Electric Power Research Institute against specific qualification criteria.
For most school bus fleets, electrifying your buses and sites will be an ongoing process with numerous procurements. In this case, you might consider establishing a multiyear contract with a vendor that can meet all your anticipated needs. Among the benefits of having an established infrastructure partner is that they can assist with the elements of site design listed in Phase Three: Step 14. of this phase. Many providers have cooperative contracts available through the Climate Mayors Purchasing Collaborative or Sourcewell.
Providers
The provider types listed below should be able to plan, provide equipment, install, maintain, and provide or connect the fleet with charge management services. Your fleet will need to select the right vendor based on your needs. Just like selecting a bus, it is best practice to talk with ESB fleets about their experiences.
Local Electrician
Contracting directly with an electrical company can work for small procurements with minimal management needs. Fleets should ensure they have a maintenance agreement or mechanism in their contract and that their vendor is certified by the Electric Vehicle Infrastructure Training Program (EVITP).
Bus Original Equipment Manufacturers
Many ESB manufacturers have partnerships with charging providers and may be able to meet all fleet charging needs through bus procurement. This can streamline procurements and ensure interoperability. Fleets using this method need to ensure they understand any service level agreements from their bus and charger provider and who they can contact if issues arise.
Charger Manufacturer
If contracting directly with a charger manufacturer, ensure the chargers are interoperable with existing ESBs or any you will procure in the future. Also inquire if their charge management software is compatible with other chargers if you have any onsite or may acquire them in the future.
Third-Party Software Provider or Electric Vehicle Service Provider (EVSP)
These vendors can provide software that is compatible with multiple chargers and buses, therefore not limiting any future procurements. They should also provide you a single point-of-contact for any charging-related issues, making them easier to resolve.
Step 18 - Utility Upgrades
With a clear charging plan in place and a contractor on board, it’s time to start the formal process for a utility service upgrade or new service, if needed. This may also be the time to complete the paperwork for any other utility programs that you identified in Phase One: Step 6 or Phase Two: Step 10. A zoning permit and plot plan showing the proposed location of utility infrastructure also might be needed.
Some charging business partners may directly pay fees and utility construction costs and may manage applying for any special utility programs.
Typical New Utility Service Request Process
-
Submit Required Documentation
Your contractor works with you to submit required forms and engineering design documents to the utility. Pay a design fee to the utility.
-
Visit Site
The utility sends a representative to meet your contractor at the site.
-
Utility Provides Project Breakdown
The utility provides a design, price, and timeline for their portion of the work. The design clearly establishes the division of responsibilities between the utility and your contractor.
-
Secure Easements
If necessary, secure easement(s) for utility equipment.
-
Authorize New Service
You authorize the utility to begin work on the new service. Expect to pay all utility construction costs in advance.
-
Complete Site Work
Your contractor completes site work to the utility’s specifications.
-
Utility Completes Work
The utility completes its portion of the work.
-
Obtain Electrical Inspection
You obtain a municipal electrical inspection.
-
Utility Energizes New Service
The utility energizes the new service. Some utilities may require a deposit.
Address Future Needs Early
If you will need a new service based on future acquisition plans, begin the upgrade process early with your utility. Grid infrastructure upgrades can take years to complete.
Plan Resources
- Joint Office of Energy and Transportation’s Clean Bus Planning Awards program – Program providing free technical assistance to eligible fleets to create bus electrification plans, including a detailed route analysis
- Joint Office of Energy and Transportation’s U-Finder – Tool for identifying utilities and incentives
- U.S. Environmental Protection Agency’s (EPA) Clean School Bus program webinar on Fleet Planning and Route Analysis – Webinar on how to perform an electric school bus route analysis
- Joint Office of Energy and Transportation’s Electric School Bus (ESB) Route Analysis Tool and instructional video – Tool for assessing ESB routes and sizing charging stations
- CALSTART’s Not Just Smart: The Importance of Managed Charging – Report on how and why to deploy managed charging in a fleet
- ESBI’s Charge Management Software Catalog – Catalog of charge management software providers and their features
- ESBI’s School Bus Electric-as-a-Service (EaaS) Directory – Catalog of firms that can offer services to aid school districts in the transition to an electric fleet
- U.S. EPA’s Clean School Bus program webinar on Incorporating Charge Management, Solar, Battery Storage, and Bidirectional Charging – Technical assistance webinar on charge management
- ESBI’s Electric Vehicle Make-Ready Guide and Table – Guide on elements of make-ready programs and directory of existing programs throughout the country
- ESBI and VEIC’s ESB Facility Assessment Guide – Step-by-step guide to assist school districts assess sites for chargers
- ESBI’s Electric School Bus Business Models Guide – Resource to help fleets identify the appropriate business model to support electrification of buses
- ESBI’s Electric-as-a-Service Directory – Directory of firms that offer services to aid fleets in bus electrification
- Sourcewell’s Electric Vehicle Equipment – Resource for ESB partner cooperative contracts
- Sourcewell’s Bus Contracts – Resource for cooperative ESB purchasing
- Climate Mayors’ Electric Vehicle Purchasing Collaborative – Resource for cooperative ESB purchasing
- ESBI’s Request for Proposal (RFP) Template – Editable template for buses and related infrastructure, planning, training, and maintenance
- U.S. Department of Energy’s (DOE)-Designated Clean Cities and Communities coalitions – Coalitions available to assist with all elements of alternative fuel transportation deployments
- Joint Office of Energy and Transportation’s Cold Weather Impacts on Electric School Buses – Fact sheet on what to consider when deploying ESBs in cold weather climates
- International Transportation Learning Center’s Providing Training for Zero Emission Buses – Guidebook for incorporating training language in RFPs
- Electric Power Research Institute’s Vetted Product List – list of charging equipment technical specifications
- Electric Vehicle Infrastructure Training Program (EVITP) – Charging station installation and maintenance training program for certified electricians
Phase Four: Implement
Overview: Implement
The implementation phase of the fleet electrification process could be the longest phase, depending on the timeline for bus delivery.
During this phase you will:
- Coordinate timelines for utility upgrades, permitting, charger installation, and ESB delivery
- Train staff who will be involved with ESBs
- Install and activate your chargers before your ESBs arrive
- Deploy your ESBs.
Step 19 - Coordinate Timelines
At this point you should clearly understand what will be required to install your charging infrastructure. You also should have started (and possibly completed) procuring chargers and ESBs. Now you need to ensure the charging infrastructure is in place and activated prior to bus delivery so the vehicles can be deployed as soon as possible.
Work with your partners to track the timelines of the four project components below. These steps might not be sequential, but rather an iterative process where you will revisit earlier steps as you progress through your plan.
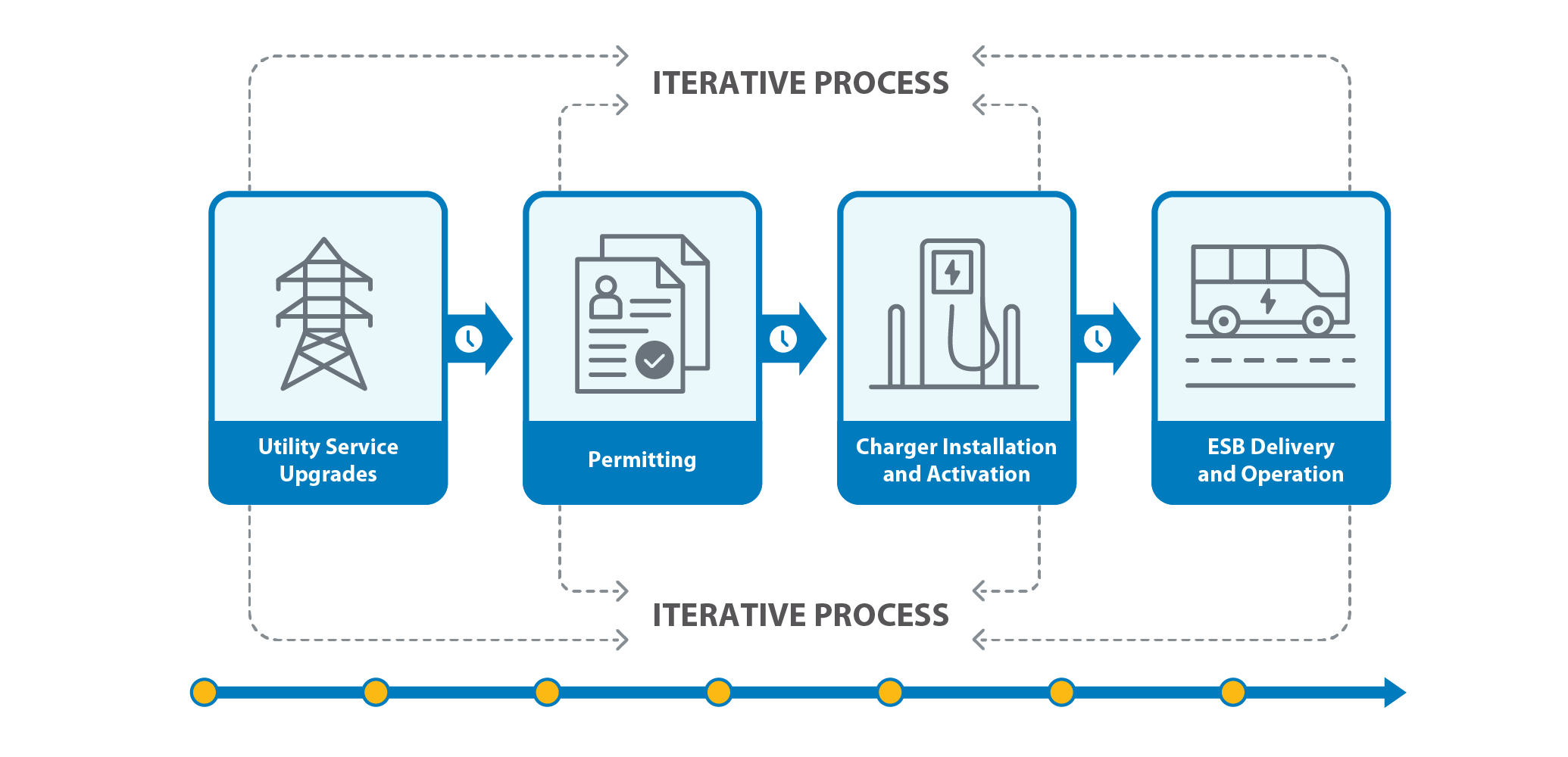
If you require utility upgrades, Phase 3: Step 18 provides resources on the process and requirements. Work with your charging provider and utility to understand the potential upgrade timeline. Permitting and charger installation can occur concurrently to save time.
If utility upgrades fall behind or will prevent you from activating your charging equipment before your buses arrive, you could consider temporary mobile charging solutions. Talk with your charging partner about possibilities.
A standard electrical permit will be required, at minimum, and some municipalities may require additional permits. Other requirements also might apply if your chargers will be available to the public.
Your charging provider should be able to apply for all permits on your behalf and provide estimated timelines for review and approval. You may also want to ask local ESB or municipal bus fleets about their experiences with permitting processes and timelines.
Your charging provider should be able to provide you with an installation timeline that includes site preparation, electrical work, equipment installation, and inspections. They will also need to verify charger operation and provide training to your staff. More details on these processes can be found in Step 21 of this phase.
Your dealer or manufacturer should be able to provide you with a delivery timeline for your ESB(s) upon issuance of a purchase order. Standard bus commissioning procedures will apply to your new ESBs. Before delivery, also confirm if there are any insurance policy changes and any additional safety inspections that may be required locally.
Step 20 - Train Staff
Effective ESB deployment involves ensuring all key stakeholders are knowledgeable about and comfortable with ESBs and charging infrastructure. This step provides an overview of recommended training components and resources for each stakeholder type.
For resources on how to create an ESB workforce development program, utilize the U.S. Environmental Protection Agency’s (EPA) Workforce Planning Recommendations and Resources. This document outlines best practices, including performing a skills gap analysis with your staff to target training needs. An additional resource is the How to Develop a Training Plan and Where To Get Certified Training webinar from the EPA’s Clean School Bus Program.
Everyone involved with your ESBs should have introductory training on ESBs and understand basic safety concepts. They should know how ESBs differ from conventional buses, how they are identified, what the labels and stickers on the bus mean, hazards of high voltage systems, and what safety precautions the buses have to protect riders from high voltage. Training and associated test materials are available through the Joint Office of Energy and Transportation’s ESB familiarization webinar series:
Drivers need to learn the unique attributes of driving an ESB, including:
- Pre-trip routines
- Start-up procedures
- Efficient driving techniques
- Regenerative braking
- Instrument cluster and icons
- Monitoring range and state-of-charge of the high-voltage battery
- Basic HVAC system operation
- Bus charging.
Your dealer or bus manufacturer should be the main source of this training, upon delivery of your ESB. Many manufacturers also have driver training videos on their YouTube channels or websites, as do other organizations. One example driver training video from Virginia Clean Cities is ESB Training Connections: Best Driving Practices. You also could consider a train-the-trainer or mentor program where internal staff can train and ride with drivers when needed.
Currently, most manufacturers require high-voltage work to be performed by their own technicians. But your technicians will need training to perform inspections, preventive maintenance, and standard repair work. This should cover:
- Components
- Personal protective equipment
- Lockout-tagout procedures
- High-voltage system disconnect and measurement
- Preventive maintenance tasks and schedules
- Troubleshooting and diagnostics.
Your dealer or bus manufacturer should be the main source of this training. Many offer 2- to 3-day sessions at customer sites, and some offer factory training.
You may also need to provide training on additional skills identified through a skills gap analysis or other avenue. Some essential technician skills for ESBs are high-voltage system safety, electrical basics, electrical measurement devices, and diagnostic/computer skills, as well as traditional vehicle skills such as suspension, steering, brakes, and low-voltage system.
Additional technician training resources include:
- National Fire Protection Association 70E Standard for Electrical Safety in the Workplace— Training offered by NFPA.org as well as other organizations that can be found online
- Automotive Service Excellence xEV—Level 1 & 2 xEV Standards and Certifications
- SAE International—SAE Course Catalog
- Electric School Bus Initiative—ESB Technician Training Database.
If in-house electricians will be repairing or maintaining charging stations, they should be certified through the Electric Vehicle Infrastructure Training Program. This program is only available to certified electricians.
All staff involved with your ESBs will benefit from understanding how your charging stations operate and basic safety principles. Basic training should cover:
- How to start and end a charging session
- Safety and hazard overview
- Correct procedures for storing and inspecting cables and connectors.
If you are incorporating charge management or plan to perform in-house repairs and maintenance, additional training could cover:
- An overview of the software and user interface
- How to monitor and identify alerts
- Preventive maintenance tasks and schedule
- Basic components and repairs.
Your charger provider should be the main source of this training.
An overview of basic charging infrastructure components and how they work is available through the Electric School Bus Initiative’s All About Charging Infrastructure video guides.
Notify your local first responders when you first decide to get ESBs so they can become trained on how to respond to incidents involving these vehicles. This training should cover:
- How to identify which buses are electric
- Emergency shut-down procedure
- High-voltage wiring and component layout
- How to remove the buses from an incident scene.
Consider inviting first responders to all the training sessions your staff attends. Resources specific to their needs include:
- National Fire Protection Association’s Emergency Response Guides and the Energy Security Agency’s Emergency Response Guides—These guides are provided by the vehicle manufacturers for most makes/models and contain important information for emergency responders
- National Fire Protection Association’s Submerged Hybrid/Electric Vehicles Fact Sheet—Information on responding to submerged electric vehicles
- Alternative Fuels Data Center’s (AFDC) EV Safety Training Resources for First and Second Responders—Central repository of available resources
- National Fire Protection Association’s EV Safety Online Training.
Your tow provider or anyone who moves buses around the yard or facilities will need training that covers:
- How to identify the ESBs
- Emergency shut-down procedure
- How to load and transport ESBs (flatbed, remove drive shaft, tow from rear)
- Considerations for damaged batteries and submerged vehicles.
Your manufacturer or dealer might provide this training upon delivery of your ESBs. Also consult the National Fire Protection Association video, EV Safety—Tow and Salvage Edition Online Training. Many of the vehicle manufacturer emergency responder guides linked in the First Responder section also include towing sections with model-specific information.
- Provide periodic refresher training as part of annual in-service training. Remind drivers they all have the potential to drive an ESB, and the more they understand the better prepared they will be to have a successful experience.
- Repeat trainings as needed to account for staff turnover.
- Ensure on-site training staff are equipped to handle future training classes. They should stay up to date on their training as ESB technology continues to evolve.
- Dispatch and routing staff need to understand ESB capabilities and limitations. Considerations include what routes they can be put on, whether you want them to verify charge status online, and whether they will be available for mid-day or afterschool routes.
- Ensure staff are aware of the effects of weather extremes on ESBs, including how range is affected by hot and cold weather. See resources from the Joint Office of Energy and Transportation for more information:
Step 21 - Install and Activate Charging Infrastructure
Your charger provider will handle charger installation and activation. To keep the project moving and on time, you should understand the steps they need to take and hold regular check-ins.
- Complete final site plan or drawings: Includes details and diagrams of any excavation work that the site or contractor will do (i.e., trenching, concrete pouring) and how this work may affect operations at the facility.
- File permit application(s): At a minimum, your site will require an electrical permit and may require other permits based on your authority having jurisdiction or the type of work being done (i.e., excavation, public land).
- Utility upgrades: Your charging provider should be in touch with your utility and coordinate upgrades with them. These upgrades can take several months, and charger installation can proceed concurrently.
- Install the charging equipment: Includes excavation and trenching, installing electrical upgrades (transformers, service panels, meters), running conduit and wires, installing the chargers, and installing site upgrades such as bollards, lighting, and signage.
- Complete the permit inspection: Perform a site inspection along with your charging provider to identify any issues or questions. Check for equipment damage, exposed wiring, charger mounting, and signage.
- Receive all commissioning documents from your charging provider. This should include the site drawing, electrical drawings and as-builts, cut sheets and owner’s manuals for all new equipment, load calculations, copies of all test reports and verification data, building permits, and inspection reports.
- Perform operation and maintenance training for your staff.
- Confirm interoperability of your buses and chargers. If your buses have not yet arrived, have your charging provider test the chargers with any available ESBs or other electric vehicles.
- If you are utilizing charging software, set up network accounts for your staff and perform training.
- Create a maintenance plan. Determine who is responsible for identifying problems with chargers and how those should be reported. Also determine who is responsible for troubleshooting and repairs.
Step 22 - Deploy ESBs
Upon receiving your ESBs, follow the tasks below in addition to your standard commissioning procedures like numbering, insurance, and safety inspections.
Update your bus operation materials to include information on your new ESBs. This new information should be available through training materials you received or planning you conducted throughout this process.
Create a new pre-trip inspection checklist for your ESBs or ask your dealer or manufacturer for a template. New items to check on an ESB include high-voltage cables, state of charge, charger connectors, and anything else recommended by your manufacturer.
In Phase 3: Step 13 , you identified optimal routes for your EBSs. Assign your ESBs to these routes or identify shorter routes for your first deployments. As your staff become more familiar with efficient driving practices and the range of your ESBs, you may be able to assign your buses to longer routes and realize additional cost savings.
Ensure your staff understand the charging requirements for your buses and they are charging as needed to complete your routes.
Implement Resources
- U.S. Environmental Protection Agency’s (EPA) Workforce Planning Recommendations and Resources – document that outlines workforce development best practices
- EPA/Joint Office How to Develop a Training Plan and Where To Get Certified Training webinar
- Joint Office of Energy and Transportation’s Webinar: Overview for Electric School Bus Operators
- Joint Office of Energy and Transportation’s Webinar: Bus Technology Overview
- Joint Office of Energy and Transportation’s Webinar: High Voltage Safety Considerations
- National Fire Protection Association 70E Standard for Electrical Safety in the Workplace— Training offered by NFPA.org as well as other organizations that can be found online
- Automotive Service Excellence xEV Level 1 & 2 xEV Standards and Certifications – training standards for medium and heavy duty EV technician training programs
- SAE International Course Catalog – catalog of training opportunities for technicians and other organization members on numerous transportation related topics
- Electric School Bus Initiative ESB Technician Training Database – catalog of resources for EV focused technician training
- Electric Vehicle Infrastructure Training Program – training program on electric vehicle charging infrastructure installation and maintenance for certified electricians
- ESBI’s All About Charging Infrastructure video guides – video series explaining the components of electric vehicle charging infrastructure
- National Fire Protection Association’s Emergency Response Guides – resource for electric vehicle emergency response guides
- Energy Security Agency’s Emergency Response Guides – resource for electric vehicle emergency response guides
- National Fire Protection Association’s Submerged Hybrid/Electric Vehicles Fact Sheet—Information on responding to submerged electric vehicles
- Alternative Fuels Data Center’s (AFDC) EV Safety Training Resources for First and Second Responders—Central repository of available resources on first responder training for EVs
- National Fire Protection Association’s EV Safety Online Training – compilation of NFPA training materials on EVs
- National Fire Protection Association’s EV Safety—Tow and Salvage Edition Online Training – video training resource for EV towing
- Joint Office of Energy and Transportation’s Hot Weather Impacts on Electric School Buses – fact sheet detailing best practices for hot weather electric school bus operation
- Joint Office of Energy and Transportation’s Cold Weather Impacts on Electric School Buses– fact sheet detailing best practices for cold weather electric school bus operation
Phase Five: Improve
Overview: Improve
Your ESBs are on the road and now it is time to evaluate their operation and maximize performance. During this phase you will:
During this phase you will:
- Develop a plan for community and student engagement
- Evaluate how your buses, chargers, and drivers are performing and identify areas to improve
- Identify if advanced technologies are right for your fleet—these could include solar and battery storage or vehicle-to-everything (V2X), also known as bidirectional charging
- Consider end-of-life options for the ESB high-voltage batteries.
Step 23 - Community and Student Involvement
Phase One: Step 4 introduced the importance of having the support of your organization and the wider community. Once buses are on the road and the fleet is familiar and confident in their capabilities, continue involving students and community members to help ensure long-term support and buy-in for ESBs.
Students can increase support for the transition to ESBs by serving as ambassadors to raise awareness about the benefits of ESBs, including heath impacts from reduced air pollution, sustainability and stewardship, and career opportunities. The Great School Electrification Challenge provides examples of how student involvement can influence decision makers.
To help students learn about ESBs, school bus fleets can share the following resources with educators to use in their classrooms:
- Highland Fleets and the Children's Environmental Literacy Foundation’s lesson plans on electrification, air quality, and environmental justice
- Electric School Bus Initiative’s lesson plan for students in grades four through eight on the circular economy and vehicle electrification
- Thomas Built Buses’ curriculum to help students engage with ESBs through multiple activities.
Maintaining open communication with members of the broader community, including the school board, caregivers, teachers, and other community members, can help strengthen support for bus electrification. This increases transparency and creates opportunities to respond to stakeholder questions and needs, thereby building trust. Tips for conducting community outreach include:
- Partner with your school district’s communications team, if they have one
- Collaborate with other fleets in your area who are also deploying ESBs to share communications resources and lessons learned about effective strategies
- Identify influential community stakeholders, their roles, and the audiences they can reach. These people can help distribute and amplify your messages.
- Determine effective messaging strategies for each type of community stakeholder, including the types of messages that will resonate with them and the best way to reach them
- Develop materials to help guide discussions for stakeholder meetings, such as school board meetings. Materials could include presentations, talking points, and answers to frequently asked questions.
Periodically evaluate your outreach activities and refine your messaging and strategies as needed. Ensure you share with community stakeholders how their input is valuable to the success of bus electrification.
Community outreach resources include:
- New York League of Conservation Voters Education Fund’s Clean Bus Guide – Information about community-wide benefits of ESBs, case studies, and stakeholders that you might want to engage.
- Alliance for Electric School Buses’ State Electric School Bus Campaigns – Map of active campaigns to promote ESBs and the organizations leading those campaigns, who could be potential community partners.
Step 24 - Evaluate Performance
Gathering ESB operation data is essential for optimizing their performance and informing future deployments. If you are utilizing networked charging or telematics, your provider may be able to generate customized reports, or you can create a tracking spreadsheet. For help organizing or interpreting data, contact the clean school bus technical assistance team at the Joint Office of Energy and Transportation. The Beaverton School District in Oregon has developed a website on their Environmental Efforts website that also provides an example for how to track ESB performance data.
- Monitor the state-of-charge (%) upon return to base. This will tell you if your buses are capable of being deployed on longer routes.
- Track your bus efficiency in kWh/mile throughout the year to identify effects from different temperatures, routes, or drivers.
- Use telematics to track regenerative braking efficiency, hard stops alerts, and hard acceleration. Combined with bus efficiency, these statistics can help you target training to adjust driver behavior or create reward programs for those that display the highest efficiency.
- Track electricity costs by monitoring utility bills.
- Calculate individual bus costs on your own, since each charging station will likely not be individually metered. Identify total kWh for each bus from your charging software or telematics and combine with the electricity costs in $/kWh to obtain per-bus electricity cost.
- Compare the costs of electricity per bus to the costs of diesel or other fuels.
- If you are subject to demand or time-of-use charges, analyze those costs and identify if you could shift times to reduce costs. Identify if charge management could help you automate the process and reduce costs.
- Track maintenance costs for your ESBs and compare them to your conventional buses in terms of cost per mile (CPM).
- Track downtime of your ESBs and identify if you need additional service support.
- Calculate emissions benefits of your ESBs through the Alternative Fuel Life-Cycle Environmental and Economic Transportation (AFLEET) Tool from Argonne National Laboratory.
- Consider installing air quality monitors in places like school entrances and bus yards to demonstrate improvements.
Track your charger downtime and identify if you need additional service support or a service-level agreement with third-party maintenance providers.
Step 25 - Investigate Advanced Technologies
Charge management is usually the simplest advanced technology to implement and often provides the most cost savings. If you are not using charge management, review Phase Three: Step 14. Other strategies for consideration are discussed below.
Supporting charging with photovoltaics (PV) and battery energy storage systems (BESS) can help bus fleets reduce demand on the grid, energy costs, and emissions. Sizing, permitting, installing, and controlling these systems is complicated, so talk with your charge management provider up front to identify their process and partners and ask for reference projects.
Resources on PV and BESS include:
- NREL’s PVWatts calculator—Allows users to estimate the size and performance of potential PV installations through a mapping tool.
- NREL’s REopt web tool—Evaluates economic viability of solar, battery storage, or other onsite energy solutions.
- NC Clean Energy Technology Center’s Database of State Incentives for Renewables & Efficiency—Contains resources for external incentives and funding for stationary energy installations.
Bidirectional charging strategies for ESBs typically utilize vehicle-to-grid (V2G) or vehicle-to-building (V2B). V2G involves utilities using bus batteries to supply power to the grid at certain times, and V2B involves bus batteries powering district buildings during outages or to reduce electricity costs through supplying electricity to buildings at high-cost times of day. ESBs can be ideal for these two strategies because of their large batteries and long dwell times (especially during the summer months).
If you are considering bidirectional charging, it is important to understand that this technology is currently in the early stages and most programs around the country are in pilot phases. Check out Bus2Grid to connect with fleets implementing bidirectional charging.
The four essential components required to start a bidirectional program include:
Bidirectional Capable Bus
Ensure that the bus(es) you are purchasing have bidirectional capabilities. If you are planning for a future bidirectional program, it is advisable to require these capabilities at the outset of your ESB transition.
Talk with your original equipment manufacturer (OEM) or dealer about how bidirectional charging will affect your high-voltage battery warranty. Some OEMs will limit bidirectional capabilities to certain thresholds like a minimum of 20–30% state-of-charge.
Bidirectional Charger
Only a couple of bidirectional chargers are currently on the market. Use the Electric Power Research Institute’s Vetted Product List to research compatible chargers. Note that the initial cost of the charger will be higher than standard chargers, and maintenance is also expected to be more complicated and costly.
Software Provider or Electric Vehicle Service Provider
You will need a partner that provides software to manage the bidirectional integration with the buses, chargers, and utility. All charge management providers should be able to provide V2X services and coordinate with utilities.
Utility Approval
Not all utilities currently allow V2X, so discuss with them before doing any planning or preparatory work. If allowed, your utility will require an interconnection agreement. All utilities have different processes and involving your software provider or having them manage the process will make it much easier. Typically, utilities will need the following to start the interconnection process: bus battery sizes, charger specifications, electrical parameters, and safety standards.
Program design will also vary across utilities. Reimbursement rates for energy usage may differ based on the level of participation from the fleet. Some utilities may offer a minimum guarantee of usage. An approval mechanism will also be in place for when the utility wants to use energy from the buses. Software providers can automate these approvals, but most pilot programs underway use manual approvals from the fleet or software provider.
If your utility does not currently offer V2X, consider a few strategies to encourage the utility to introduce V2X:
- Develop support for V2X through your school association, governor’s office, and public utility commission.
- Develop a quick explanation of how V2X can be valuable not only to the fleet but also to the utility. Let them know how much power and energy may be available from your buses.
- Remember that school districts are a very large and important customer in any utility region and that utilities are tasked with serving their customers. Don’t take your first “No” as their final decision.
Step 26 - Battery End-of-Life
High-voltage batteries should last the life of your bus, and most are now warrantied for 8–12 years. Bus fleets have some options about what can be done at battery end-of-life. Start considering this during bus procurement when your OEM or dealer may take ownership of the process and provide transportation, disassembly, repurchasing, or value assessment.
Disposal in a landfill is not an option for lithium-ion batteries because they pose a risk of fire and release of toxic materials to the environment. The two options at end-of-life are:
A vehicle battery still has considerable value in stationary storage even at its “end-of-life” point in the vehicle itself. Benefits of using used high-voltage batteries as storage to power chargers, depots, or schools can be extensive, including:
- Reducing peak demand, which is your highest kW usage and can come with very high electricity costs if you are subject to demand charges. If peak demand occurs during mid-day and you are looking to lower it, you can charge your stationary batteries at night and then use them in combination with the grid during mid-day to cut usage and therefore costs.
- Using second-life batteries to reduce peak demand may also allow you to forgo grid upgrades, which can be extremely expensive. Second-life batteries may also enable faster charging at sites with low voltage.
- Reducing total scope emissions by charging batteries when the grid is powered by clean energy or reducing grid usage at high-demand times when higher-emitting peaker plants are in use.
- Using second-life batteries as backup generators for schools, shelters, and other buildings.
All batteries will eventually need to be recycled, and it is important to understand your options and associated costs. The Lithium-Ion Battery Supply Chain Database contains a list of recyclers in the United States, as well as other companies involved in the battery supply chain.
Battery recycling is performed by:
- Reclaiming the critical materials that are not only expensive and rare but also raise concerns about harmful mining practices. Recyclers must separate all the material in lithium metal oxides for them to be reused.
- Direct recycling technology (under development) where recyclers will recover, regenerate, and reuse battery components without breaking down the chemical structure. This approach can lower recycling costs, thereby lowering the cost of new batteries
Improve Resources
- The Citizens’ Climate Lobby’s National Youth Action Team’s Great School Electrification Challenge—Program where students and school boards pledge to “electrify everything” in their schools
- Highland Fleets and the Children's Environmental Literacy Foundation’s lesson plans—Course curriculum on electrification, air quality, and environmental justice
- Electric School Bus Initiative’s lesson plan—Curriculum for students in grades four through eight on the circular economy and vehicle electrification
- Thomas Built Buses’ curriculum—Curriculum to help students engage with ESBs through multiple activities
- New York League of Conservation Voters Education Fund’s Clean Bus Guide—Information about community-wide benefits of ESBs, case studies, and stakeholders to engage
- Alliance for Electric School Buses’ State Electric School Bus Campaigns—Map of active campaigns to promote ESBs and the organizations leading those campaigns who could be potential community partners
- Beaverton, Oregon, School District’s Environmental Efforts—School district that displays ESB performance data
- Argonne National Laboratory’s Alternative Fuel Life-Cycle Environmental and Economic Transportation (AFLEET) Tool—Emissions calculator tool
- National Renewable Energy Laboratory’s (NREL) PVWatts calculator—Allows users to estimate the size and performance of potential PV installations through a mapping tool
- NREL’s REopt web tool—Evaluates economic viability of solar, battery storage, or other onsite energy solutions
- NC Clean Energy Technology Center’s Database of State Incentives for Renewables & Efficiency—Contains resources for external incentives and funding for stationary energy installations
- Bus2Grid—Organization of school bus fleets implementing bidirectional charging
- Electric Power Research Institute's Vetted Product List—Resource with charger specifications and compliance details for multiple national and state-level programs
- NREL’s Lithium-Ion Battery Supply Chain Database—List of recyclers in the United States, as well as other companies involved in the battery supply chain