Batteries for Electric Vehicles
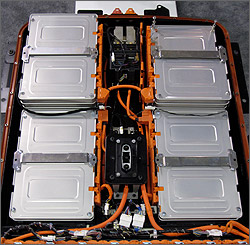
Most plug-in hybrids and all-electric vehicles use lithium-ion batteries like these.
Energy storage systems, usually batteries, are essential for all-electric vehicles, plug-in hybrid electric vehicles (PHEVs), and hybrid electric vehicles (HEVs).
Types of Energy Storage Systems
The following energy storage systems are used in all-electric vehicles, PHEVs, and HEVs.
Lithium-Ion Batteries
Lithium-ion batteries are currently used in most portable consumer electronics such as cell phones and laptops because of their high energy per unit mass and volume relative to other electrical energy storage systems. They also have a high power-to-weight ratio, high energy efficiency, good high-temperature performance, long life, and low self-discharge. Most components of lithium-ion batteries can be recycled, but the cost of material recovery remains a challenge for the industry. Most of today's all-electric vehicles and PHEVs use lithium-ion batteries, though the exact chemistry often varies from that of consumer electronics batteries. Research and development are ongoing to reduce their relatively high cost, extend their useful life, use less cobalt, and address safety concerns in regard to various fault conditions.
Nickel-Metal Hydride Batteries
Nickel-metal hydride batteries, used routinely in computer and medical equipment, offer reasonable specific energy and power capabilities. Nickel-metal hydride batteries have a much longer life cycle than lead-acid batteries and are safe and abuse-tolerant. These batteries have been widely used in HEVs. The main challenges with nickel-metal hydride batteries are their high cost, high self-discharge rate, heat generation at high temperatures, and the need to control hydrogen loss.
Lead-Acid Batteries
Lead-acid batteries can be designed to be high power and are inexpensive, safe, recyclable, and reliable. However, low specific energy, poor cold-temperature performance, and short calendar and lifecycle impede their use. Advanced high-power lead-acid batteries are being developed, but these batteries are only used in commercially available electric vehicles for ancillary loads. They are also used for stop-start functionality in internal combustion engine vehicles to eliminate idling during stops and reduce fuel consumption.
Ultracapacitors
Ultracapacitors store energy in the interface between an electrode and an electrolyte when voltage is applied. Energy storage capacity increases as the electrolyte-electrode surface area increases. Although ultracapacitors have low energy density, they have very high power density, which means they can deliver high amounts of power in a short time. Ultracapacitors can provide vehicles with additional power during acceleration and hill climbing and help recover braking energy. They may also be useful as secondary energy-storage devices in electric vehicles because they help electrochemical batteries level load power.
Recycling Batteries
Electric vehicles are relatively new to the U.S. auto market, so only a small number of them have approached the end of their useful lives. As electric vehicles become increasingly common, the battery recycling market may expand.
Studies have shown that an electric vehicle battery could have at least 70% of its initial capacity left at the end of its life if it has not failed or been damaged. The remaining capacity can be more than sufficient for most energy storage applications, and the battery can continue to work for another 10 years or more. Many studies have concluded that end-of-life electric vehicle batteries are technically feasible for second-use applications such as stationary grid and backup power applications. Although there are viable business models for high-value, small, and niche applications for second-use batteries (i.e., powering forklifts and portable devices, replacing diesel backup generators, acting as after-market replacement packs for electric vehicles), the economic viability of installing second-life batteries is still evolving. Costs associated with the purchase price of end-of-life batteries include transportation, storage, sorting and testing, remanufacturing, reassembly and repurposing, integration into battery energy storage systems, certification, and installation.
Widespread battery recycling would help keep hazardous materials from entering the waste stream, both at the end of a battery's useful life and during its production. The U.S. Department of Energy is also supporting the Lithium-Ion Battery Recycling Prize to develop and demonstrate profitable solutions for collecting, sorting, storing, and transporting spent and discarded lithium-ion batteries for eventual recycling and materials recovery. After collection of spent batteries, the material recovery from recycling would also reintroduce critical materials back into the supply chain and increase the domestic sources for such materials. Work is now underway to develop battery recycling processes that minimize the life cycle impacts of using lithium-ion and other kinds of batteries in vehicles. But not all recycling processes are the same, and different methods of separation are required for material recovery.
To recover valuable materials from lithium-ion batteries, there are three major technologies currently in different stages of commercialization: smelting (pyrometallurgy), chemical leaching (hydrometallurgy), and direct recycling. In addition to these methods, mechanical treatment through disassembly, crushing, shredding, and separation to create what is called black mass is a major element of any recycling technology.
- Smelting (pyrometallurgy) is the process of high-temperature thermal treatment of batteries in a furnace to extract metals and intermediate salts. These can be further processed to create battery-grade precursors that could go to cathode processing facilities. Smelting (pyrometallurgy) facilities are operational on a large scale and can accept multiple kinds of batteries, including lithium-ion and nickel-metal hydride. During high-temperature processing, organic materials, including the electrolyte and carbon anodes, are burned as fuel or reductant. The valuable metals and intermediate salts are recovered and sent to refining storage make them into a product suitable for any use, including battery grade processing. The other materials, including lithium, are contained in the slag, which is used as an additive in concrete. Smelting burns a significant amount of energy.
- Chemical leaching (hydrometallurgy) is a process using chemical treatment to extract key compounds from the black mass, including lithium compounds. The process uses leaching fluids such as inorganic acid, organic acid, alkali, or even bacteria solutions that dissolve metals in cathodes to salts that can be used as precursors to make new cathodes. Many companies in the United States and around the world are building factories for hydrometallurgy because of lower capex and flexibility to directly produce cathodes. In the next few years, several facilities will come online to recycle the onslaught of batteries being retired.
- Direct recycling involves the recovery of cathodes while maintaining its molecular structure rather than breaking it down into constituent metals for reprocessing into battery-grade cathode. Eliminating the need for smelting or chemical leaching makes the prospect of direct recycling most economically viable. With improvement in efficiencies and at-scale production of cathodes of the future, direct recycling factories could be a viable option.
Separating the different kinds of battery materials is often a stumbling block in recovering high-value materials. Therefore, battery design that considers disassembly and recycling is important for the sustainability of electric vehicles. Standardizing batteries, materials, and cell design would also make recycling easier and more cost-effective.
See the report: Technical and Economic Feasibility of Applying Used EV Batteries in Stationary Applications.
More Information
Learn more about research and development of batteries from the National Renewable Energy Laboratory's energy storage pages and the U.S. Department of Energy Vehicle Technologies Office's batteries page.